Schneider Electric Launches Smart Manufacturing Concept to Industry Players in EA
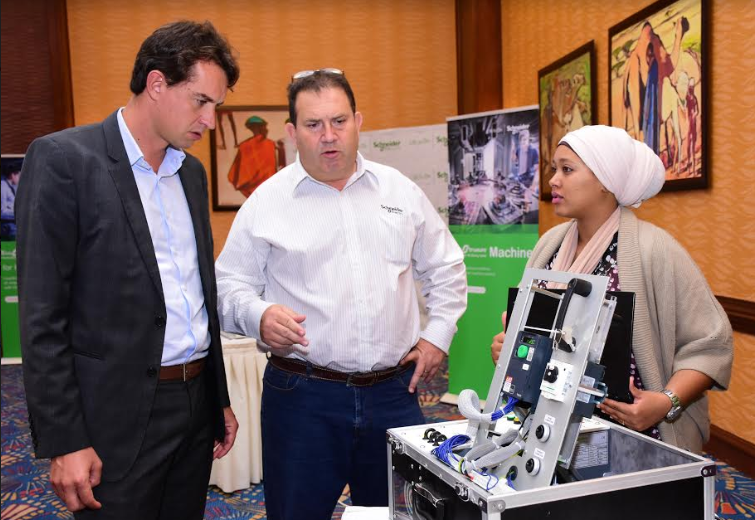
Schneider Electric, the leader in digital transformation of energy management and automation, is deploying its “Smart Factory” program to the East African market.
The Schneider smart factory concept showcases how digital transformation delivers improvements in the efficiency, to reduce time and costs, operator errors and provide better support to the end user in the day-to-day operations and maintenance of the industries through better visibility of the operations.
According to the Government’s Big 4 Agenda, the share of the manufacturing sector should rise to 15% of GDP by 2022. To close this gap, industries need to start looking at transformative strategies that will lead to overall manufacturing and operation efficiencies.
As a leader in digital transformation, Schneider Electric launched “Smart Manufacturing” program, powered by EcoStruxure for Industry and opened its doors to share its knowledge and best practices in order to address customers’ pain points in the transformation journey; driven by IoT monitoring, collaborative documentation and maintenance, unified operations centres, electrical safety and customized operator training, digital scheduling and capture of calibration records to meet compliance requirements, remote assistance for maintenance & predictive maintenance via cloud enabled machine learning.
As the world becomes more digitized industry players must focus on the question of how to build a smart factory. Digital transformation throughout the industrial value chain is critical to achieving increased global competitiveness.
Read: Schneider Electric – Powers Village to Global School in Vihiga County
Smart Factories will enable:
- Mass personalization. To meet the challenges from production efficiency, profitability, and more detailed needs of customer, traditional factory is looking for the way to produce more personalized goods to answer to a more versatile demand and to different customer segments
- Increased quality. Digitization leads to a new approach in business models. The customers are also owning new types of usage and industries need to offer higher quality and services associated to their goods.
- Reduced energy costs. 200% faster growth of electricity demand compared to energy demand by 2040. Energy has become an increasing part of the total costs of running a factory, and reducing the environmental footprint of the factory is a growing concern – digitization is the answer to both.
- Operational excellence. 80% of failures remain purely random and are stopping production in a very unplanned way. traditional factory needs digital tool and solutions to realize predictive maintenance which allows to identify deviations vs models and anticipate failures
- Change of mindset. is the basic for successful digital transformation which gives the power back to the person who is piloting the machine.
“Factories that have successfully deployed Smart Factory solutions powered by EcoStruxure for Industry have improved 8~10% productivity yearly with process optimization, and recorded energy efficiency improvement of 5~8% yearly. This provides a case for traditional industry players to start considering the move to smart manufacturing.” noted Edouard Heripret, General Manager, Schneider Electric East Africa.
Read: Schneider Electric Unveils Digital Architecture For Energy Management In Buildings
Plants have achieved remarkable results in the following four areas:
- Agile Management and Process Efficiency: Operational transparency and visibility to facilitate root cause analysis; paperless operations to decrease non-value-added cost; enhanced reactivity by faster response to both internal (shop floor) and external customer needs
- Asset Performance and Reliability: Critical equipment and facility data collection and analysis to prevent unexpected breakdowns; critical process data collection and analysis to increase process reliability; increased maintenance effectiveness
- Energy Efficiency: Visualize, control, and optimize power consumption and costs; Power Advisor to support energy efficiency
- Empowered Operators: Empowering operators to make more effective response to the factory floor in terms of safety, quality, on-time delivery, and efficiency through short interval management; and empowering maintenance teams with real-time machine and facility performance, maintenance document visualization, and remote expertise support when needed
Smart Manufacture solution integrates technologies of lean manufacturing, automation, and digital to enable full data transparency, visibility and traceability throughout the lifecycle of production and operation, as well as energy consumption. We enable operators and decision makers to receive the right information at the right time to make the best optimization decisions.
Read: Schneider Electric Launches New Stand-alone Pay-As-You-Go Electricity Solution
Schneider Electric implements the EcoStruxure solutions in a multitude of its own manufacturing facilities across the world to help optimize the manufacturing processes and energy consumption. These factories provide visual management tools to empower employees in their daily tasks to drive performance.
Schneider’s Smart Factories deploy solutions under its EcoStruxure architecture and include connected products, edge control and apps, analytics & services for energy management: Augmented Operator Advisor, Power Monitoring Expert, IoT monitoring via Machine Advisor, Facility expert for collaborative documentation and maintenance, Unified Operations Centres, Electrical Safety and customized operator training, Collaborative Robots, digital scheduling and capture of calibration records to meet compliance requirements, remote assistance for maintenance & Predictive maintenance via cloud enabled Machine learning.
For all the latest technology and business news from Kenya and the world, follow us on Twitter and like us on Facebook.